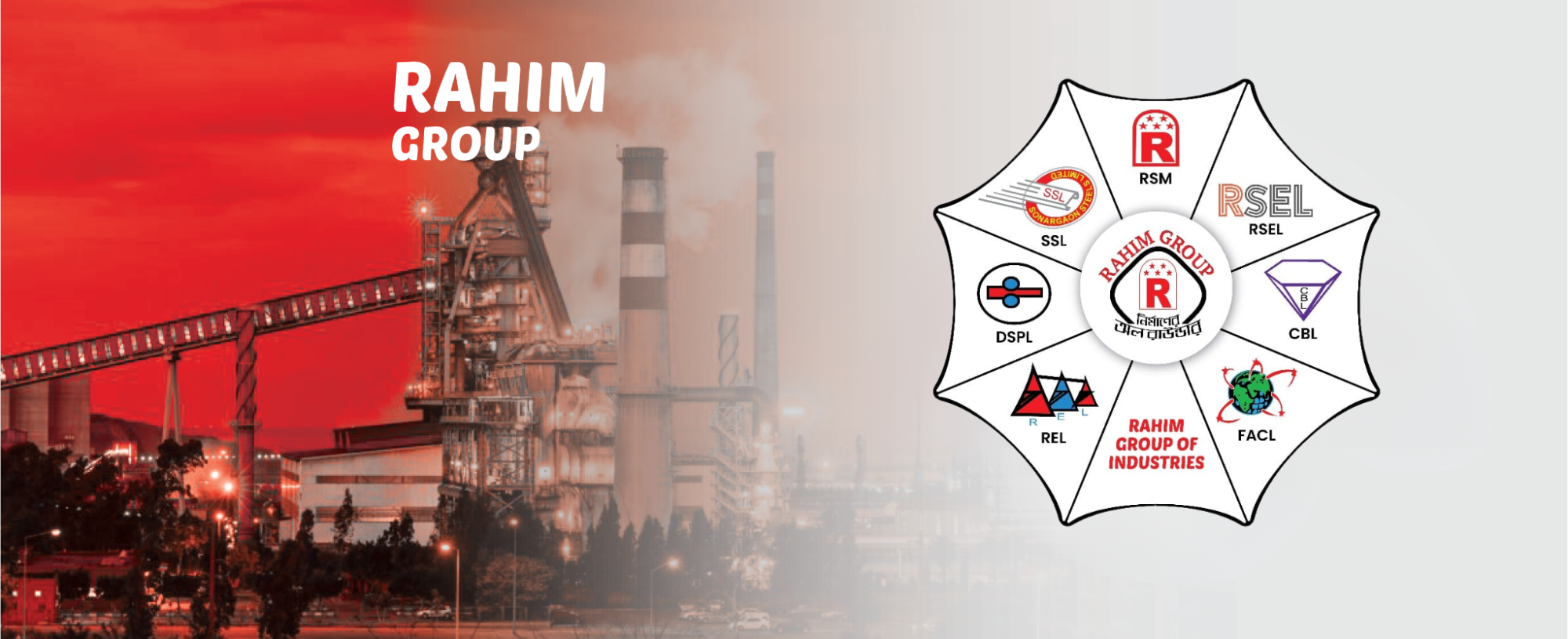
DIAMOND STEEL PRODUCTS CO. (PVT.) LTD
Owning to the success of the re-rolling mill and high customer demand, a second mill was established in 1976 at Shyampur, known as Diamond Steel Products Private Company Limited.
RSM B300A-R(40)
Mechanical Property :
Steel Grade | Standard | Frog Mask | Yield Strength (Mpa) | Ts/Ys ratio | Elongation%(G.L = 5D) | EMF% |
---|---|---|---|---|---|---|
Min | Min | Min | Min | |||
300A-R | BDS ISO 6935-2:2016 | RSM 40// Dia // B300A-R | 300 | 1.02 | 16 | 2 |
Chemical Property :
Steel Grade | Standard | Frog Mask | C%(Max) | mn% (Max) | Sl%(Max) | S%(Max) | P%(Max) | CEV%()Max |
B300A-R | BDS ISO6935-2:2016 | RSM//Dia//B300A-R | – | – | – | 0.060 | 0.060 | – |
Billet Reheating and Hot Rolling
* This process initially start from the Re-heating furnace.
*Stacking of billets is done on the hot charging area through overhead crane.
*Continuous pushing of billets, that are placed parallel to each other, is then followed through hydraulic or mechanical pusher.
*Different zones are divided in the furnace depending on the capacity of hourly heating for temperature control.
*The billets are then heated to their discharge temperature through air along with colossal burners in the furnace.
Application
RSM B300A-R(40) | Applicable in low rise structure where dynamic load is not considerable. It has the wide application in pile and slab construction |
RSM Deformed Bar Reckoner
Nominal Diameter(mm) | Anno (mm²) | Kg/Meter | Permissible Deviation(%) | Meter/Ton | Feet/Ton |
8 | 50.3 | 0.395 | ±8 | 2531.6 | 8313 |
10 | 78.5 | 0.617 | ±6 | 1622 | 5320 |
12 | 113 | 0.888 | ±+ | 1126.4 | 3694 |
16 | 201 | 1.58 | ±5 | 633.6 | 2078 |
20 | 314 | 2.47 | ±5 | 405.5 | 1330 |
22 | 380 | 2.98 | ±4 | 335.1 | 1099 |
25 | 491 | 3.85 | ±4 | 259.5 | 851.2 |
28 | 616 | 4.84 | ±4 | 206.9 | 678.6 |
32 | 804 | 6.31 | ±4 | 158.4 | 519.5 |
40 | 1257 | 9.86 | ±4 | 101.4 | 332.5 |
Bend & Reband Test Requirement :
Standard | Nominal Bar Diameter, D (mm) | Mandrel Diameter (Max) | Standard | Mandrel Diameter (Max) | ||
Ben ( 160-180) | Rebend | Ben ( 180) Grade 60 (420) | Ben ( 180) Grade 80 (550) | |||
8 | 3D | 5D | 3D | 3.5D | ||
10 | 3D | 5D | 3D | 3.5D | ||
12 | 3D | 5D | 3D | 3.5D | ||
16 | 3D | 5D | ASTM A706/A706M | 3D | 3.5D | |
BDS ISO 6935 – 2:2016 | 20 | 6D | 8D | 4D | 5D | |
22 | 6D | 8D | 4D | 5D | ||
25 | 6D | 8D | 4D | 5D | ||
28 | 6D | 10D | 6D | 7D | ||
32 | 6D | 10D | 6D | 7D | ||
40 | 6D | 10D | 8D | 9D |