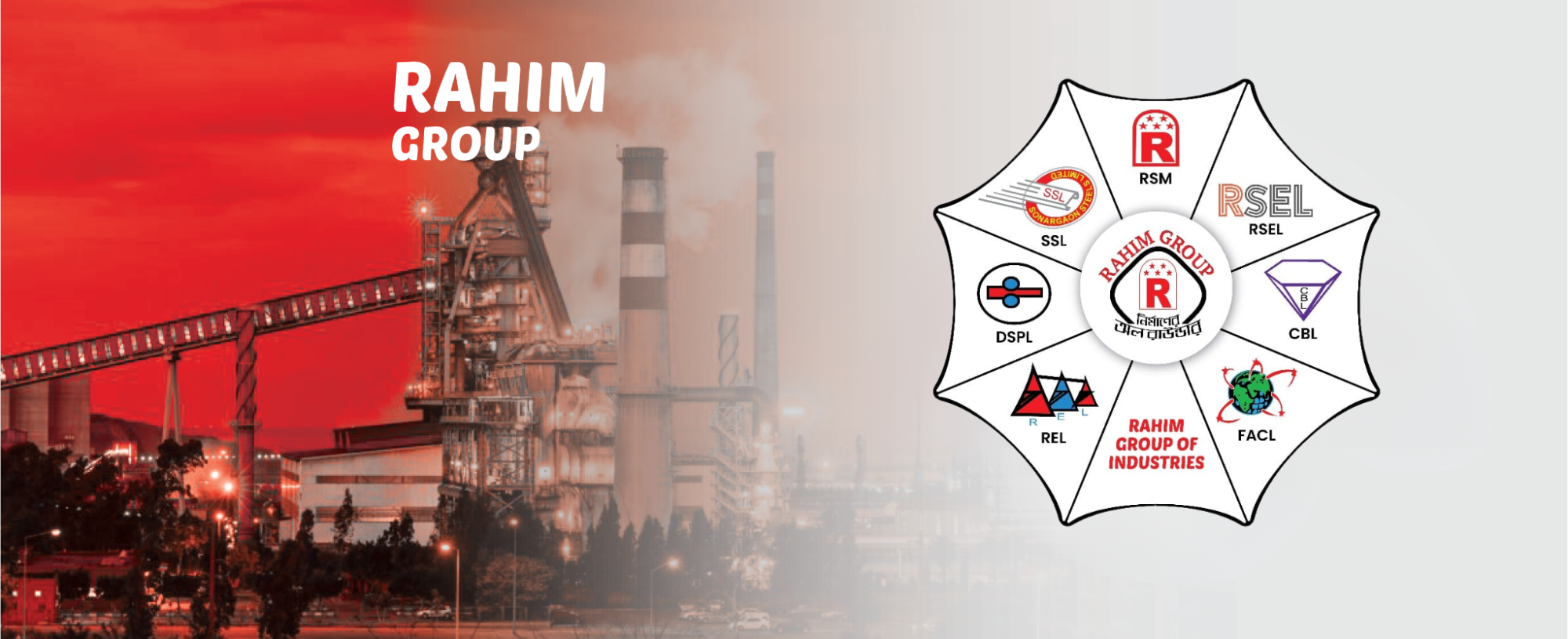
Why Rahim Steel RSM B420DWR?
The first “B” stands for steel for reinforcing concrete. The next 3 digits represent the specified characteristics value of minimum upper yield strength. The fifth symbol stands for ductility class. The sixth symbol “W” means intended for welding. The last “R” stands for ribbed bar.
Salient Features of Ductility Class “D”:
- According to BDS ISO 6935-2:2016, the highest ductility class is “D” among the four ductility class. The Elongation at Maximum Force (EMF) is 8% in this class, which is very much effective in earthquake prone zone.
- The ratio of tensile strength and yield strength (TS/YS) is minimum 1.25, which is one of the major requirements of American Concrete Institute (ACI) and Bangladesh National Building Code (BNBC) especially on earthquake prone zone.
- Due to its maximum yield strength range, the structural designers will have a great flexibility on yield point (fy) design.
- The major provisions of the Ductility class “D” are complying with Low Alloy Steel Standard: ASTM A706/A706M, which is widely acceptable by the structural engineers.
Billet & Slab Making in Rahim Steel Plant
Steel is a dynamic, versatile and eco-friendly product with diverse use and applications. The raw materials which are used for making steel are steel scrap, sponge iron and Hot Briquetted Iron (HBI). Sponge Iron and Hot Briquetted Iron (HBI) are imported from abroad.
Sponge iron/HBI and steel scrap charged into the induction furnace in a specific ratio. After the complete melting of charge, the hot liquid metal samples are taken to analyze the chemical ingredients present, i.e. carbon, manganese, silicon, phosphorous, sulphur etc.
Oxides are formed in the furnace which are lighter than molten steel and therefore float above as slag. This slag primarily contains impurities, that are extracted by tilting the furnace in 15 degrees angle.
Ladle Furnace is the second stage of steel refining. After removing the impurities, samples of the molten steel is collected and send to the laboratory for chemical composition evaluation. Depending on the results, necessary amount of refining additives are added. In the LRF the molten steel is reheated by arcing again with graphite electrode. A second sample is then collected and analyzed for adding necessary Ferro- Alloy to produce particular grade of steel. During final stage of refining argon gas is blown through the molten steel to eliminate the remaining impurities and homogenize the composition of the steel.
The temperature of liquid metal is raised to 1600-1650 degree centigrade for casting. For billet casting, the liquid steel is poured into the ladle and the ladle is then taken to Continuous Casting Machine – CCM for billet casting.
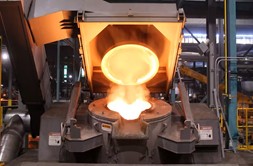
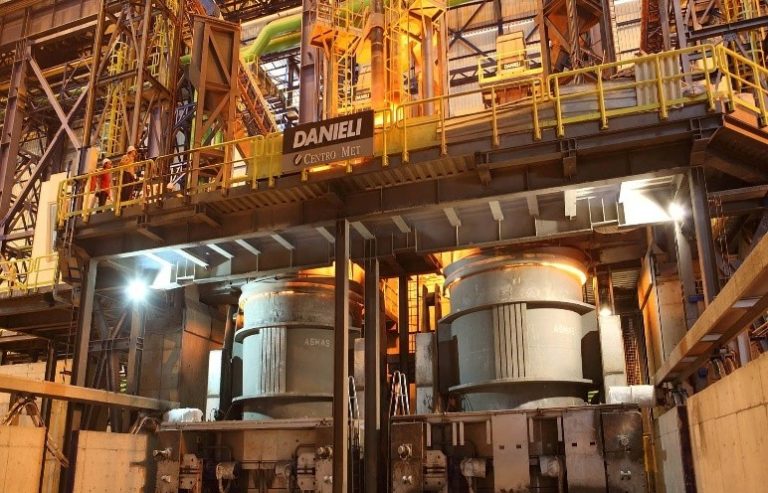
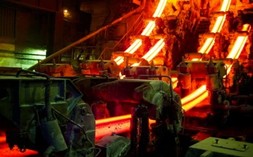
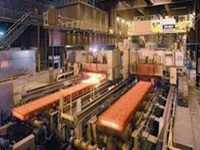
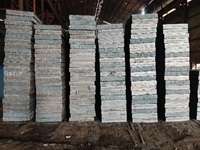
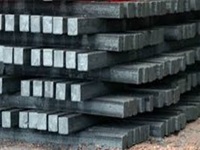
Rahim Steel Mills Co. Pvt. Ltd.
RSM B420DWR
Mechanical Property:
Steel Grade | Standard | Frog Mark | Yield Strength (MPa) | TS/YS Ratio | Elongation% (GL = SD) |
| |
Min | Max | Min | Min |
| |||
B420DWR | BDS ISO 6935-2:2016 | RSM// Dia // B420DWR | 420 | 1.3xYS(min) | 1.25 | 16 |
Chemical Property:
Steel Grade | Standard | Frog Mark | C% (Max) | Mn% (Max) | Si% (Max) | S% (Max) | P% (Max) | CEV% (Max) |
B420DWR | BDS ISO 6935-2:2016 | RSM// Dia // B420DWR | 0.30 | 1.50 | 0.55 | 0.040 | 0.040 | 0.56 |
Rahim Steel TMT Process
RAHIM STEEL is using the world prominent latest STS technology to develop Thermo Mechanically Treated (TMT) rebars. The deformed bars are produced in state-of-the-art plants under the close supervision of high-caliber metallurgists and engineers. RSM B420DWR rebars are hot rolled from steel billets and subjected to PLC controlled on line thermo mechanical treatment in three successive stages.
Quenching: The hot rolled bar leaving the final mill stand is rapidly quenched by high pressure water in special venturi tubes. This hardens the surface of the bar to a depth optimized for each section through formation of magnetic rim, while the core remains hot and austenitic.
Self Tempering: As the bar leaves the quenching venturi tube the core remains hot compared to the surface, allowing heat to flow from the core to the surface which causes tempering of the outer martensitic layer into a structure called Tempered Martensite. The core still remains austenitic at this stage.
Atmospheric Cooling: This takes place on the cooling bed, where the austenitic core is transformed into a ductile ferrite-pearlite structure. Thus the final structure consists of an optimum combination of strong outer layer (tempered martensite) with a ductile core (ferrite-pearlite). This gives RSM rebars a unique combination of high strength and ductility.
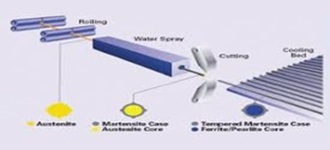
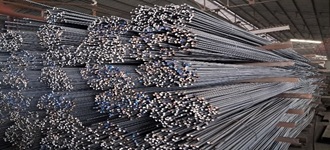
Application
Rahim Steel RSM B420DWR | Due to its higher uniform elongation and excellent bend ability, it could be used in all type of RCC structures as well as earthquake prone zone. It is now widely used in various government projects of PWD, LGED, RHD, DPHE, EED, RAJUK, WASA, City Corporation, MES etc. |
Rahim Steel Mills Co. Pvt. Ltd.
RSM 60 (420)
Mechanical Property:
Steel Grade | Standard | Frog Mark | Yield Strength (MPa) | UTS (MPa) | TS/YS Ratio | Elongation% (G.L=8* or 200mm) | ||
Min | Max | Min | Max | Min | ||||
60 | ASTM A706/A706M | RSM 60//Dia//420 | 420 (60000 PSI) | 540 (78000 PSI) | 550 (80000 PSI) | —- | 1.25 | (10,12,16,20) mm: 14% (22.25,28,32) mm: 12% |
60 | ASTM A615M | RSM 60//Dia//420 | 420 (60000 PSI) | ——- | 620 (90000 PSI) | —– | —— | (10,12,16,20) mm: 9% (22,25) mm: 8% (28 to above) mm: 7% |
Chemical Property:
Steel Grade | Standard | C% (Max) | Mn% (Max) | Si% (Max) | S% (Max) | P% (Max) | CEV% (Max) |
60 | ASTM A706/A706M | 0.30 | 1.50 | 0.50 | 0.045 | 0.035 | 0.55 |
60 | ASTM A615M | ——- | ——- | ——– | 0.060 | 0.060 | 0.55 |
Billet Reheating and Hot Rolling
- This process initially starts from the Re-heating furnace.
- Stacking of billets is done on the hot charging area through overhead crane.
- Continuous pushing of billets, that are placed parallel to each other, is then followed through hydraulic or mechanical pusher.
- Different zones are divided in the furnace depending on the capacity of hourly heating for temperature control.
- The billets are then heated to their discharge temperature through air along with colossal burners in the furnace.
- Through Ejectors the material is drawn out once the billet has reached the “Discharged Door” and moreover the computer system has determined that the billet has been effectively heated.
After this process, rescaling is carried out. This is done by passing the billet all the way through the rescaling unit. Pressurized water is used to dispatch the thick layer of oxidized iron collected at the surface of the billet during the stage inside the reheat furnace. After successful rescaling, the billet has to go through slitting systems. These are mainly utilized for permitting the rolling of rebars in several stands. This helps in augmenting the productivity of rebars of small size considerably, keeping the speed of finishing constant.
The process is further continued with roughing. For this, a roughing mill is used, which is made up of different independent rolling stands. Rolling of billets, that are heated in the furnace, is done continuously till they obtain bright orange-yellow color. After this, high pressure water jets are used for cleaning of scale or oxidized iron.
The thickness of the leading edge of the bar is then estimated once the transfer bar exits the final roughing mill stand. The temperature profile, from top to bottom, of the produced bar is then measured by a pyrometer.
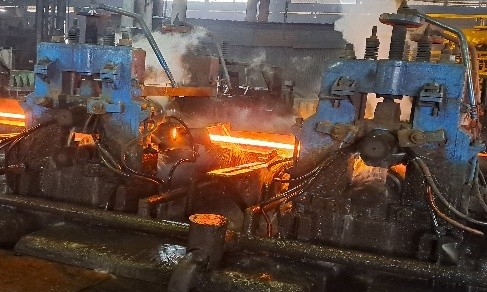
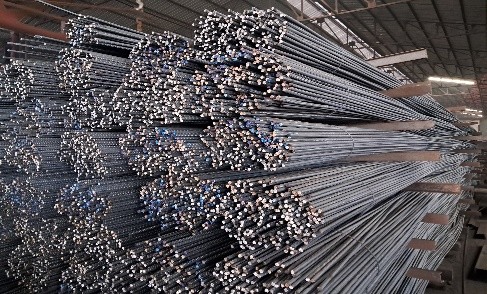
Application
Rahim Steel RSM 60 (420) | Suitable for all kinds of RCC structures where high bond value with concrete and high strength is desired. |
Rahim Steel Weight Table of Ribbed Bar
Normal Dia (MM) | Actual Dia (MM) | Unit Weight (KG/M) | ||
Min. | Max. | Min. | Max. | |
8 | 7.8 | 7.95 | 0.375 | 0.390 |
10 | 9.8 | 9.95 | 0.592 | 0.610 |
12 | 11.8 | 11.95 | 0.858 | 0.880 |
16 | 15.8 | 15.95 | 1.540 | 1.568 |
20 | 19.8 | 19.95 | 2.417 | 2.454 |
22 | 21.8 | 21.95 | 2.930 | 2.970 |
25 | 24.8 | 24.95 | 3.792 | 3.838 |
28 | 27.8 | 27.95 | 4.765 | 4.816 |
32 | 31.8 | 31.95 | 6.235 | 6.294 |
40 | 39.8 | 39.95 | 9.766 | 9.840 |
Rahim Hot Plate Mill
We are the only manufacturer of Hot Rolled MS Plates (06 mm to 30 mm) in Bangladesh, which are suitable for Ship, Oil tanker, LPG Cylinder, Structural fabrication, Railway wagon and so on.
Production Process of Rahim MS Plate:
1. Raw Material: Slabs size of (1240 x 900 x 115) mm act as the raw material for the MS Plate. We use an automatic cutting machine to prepare the slab.
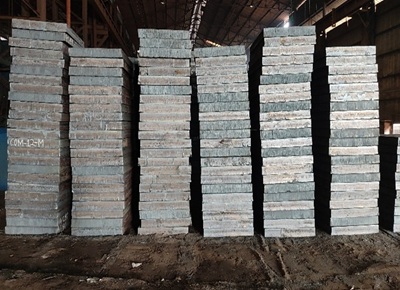
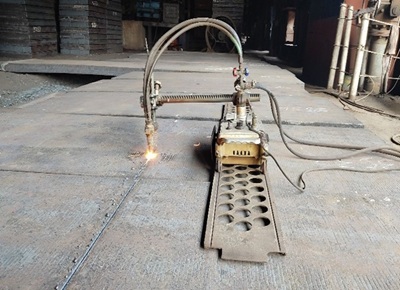
2. Softening the Slab by the Reheating Furnace: Two re-heating furnaces of latest technology are used to soften the slabs with the extreme temperature of 1350°C.
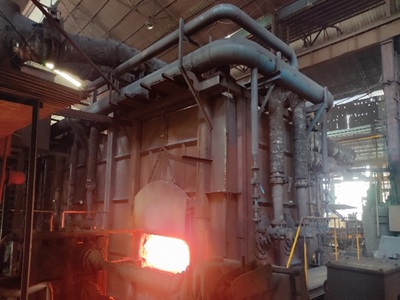
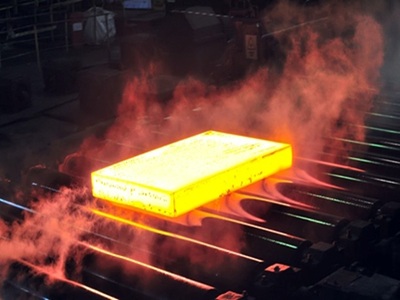
3. Descaling: The slab passes through the primary and secondary descaling operations at this step. Treated water is applied to the slab and plate surfaces sprayed at 160 and 200 bar of pressure, two high-pressure descaling pumps work together to produce this tremendous water pressure.
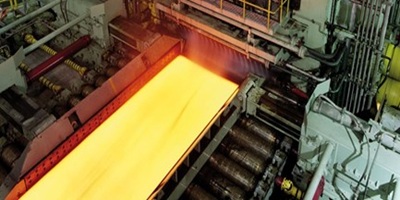
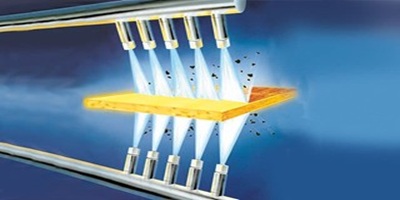
4. Rolling: The heated softened slab goes into a two high rolling mill, which is powered by 3000 HP DC motor, where the slabs turn into plate. Thanks to our mighty and the largest rolling stand in Bangladesh.
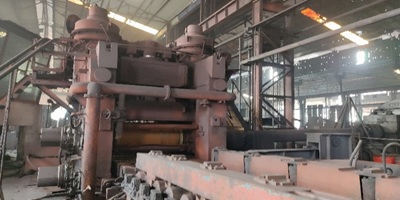
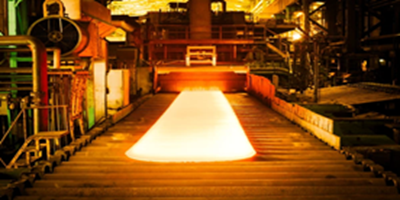
5. Cutting and Primary Sizing: After rolling we cut the plate by a powerful Shearing Machine. We cut the half round shaped head of plate and do primary sizing at this step.
6. Leveling: At this step, plate goes into a leveler machine to level and get the desired surface of the plate.
7. Trimming: After cooling the plate is trimmed by a Trimming Machine, to get desired width and delicate edges of plate.
8. Final Sizing: This is the final step of the process. Where we cut the plate as per our customer demand.
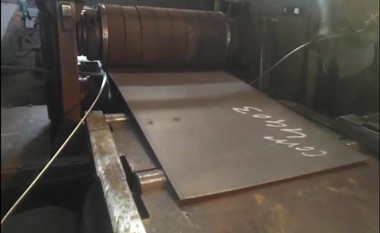
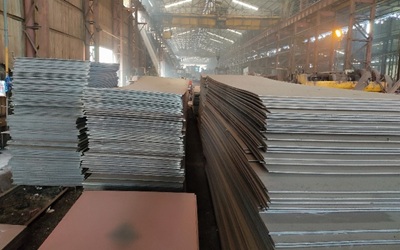
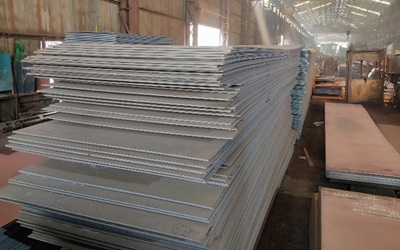
Rahim Steel Mills Co. Pvt. Ltd.
The most reliable and versatile manufacturer of quality HOT ROLLED PLATE & SHEETS in Bangladesh
Rahim MS Plate
(CG)
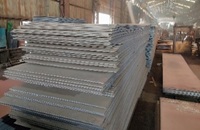

Rahim MS Plate
(GL)
Chemical Composition and Physical Properties of Rahim M.S. Plate
Specification | Grade | C% (max) | Mn% (max) | P% (max) | S% (max) | Si% (max) | Al% (max) | N(ppm) (max) | YS (min) N/mm2 | UTS (min) N/mm2 | Elong% GL-200mm | Application |
Lloyds | DNV VL-A | 0.21 | 2.5xc% | 0.035 | 0.035 | 0.50 | —– | —- | 235 | 400-520 | 16 | Ideal for structural works such as Ships, Oil tanker/storage and other constructions where dynamic load and weld ability are prime factors. |
JIS G3116 | SG225 SG295 SG325 SG365 | 0.20 | 0.30(min) 1.0(max) 1.50(max) 1.50 | 0.040 0.040 0.040 0.040 | 0.040 0.040 0.040 0.040 | —– 0.35 0.55 0.55 | —– | —- | 255 295 325 365 | 400 440 490 540 | 28 26 22 20 | Suitable for LPG Cylinders. |
ASTM | A-36 | 0.25 | 1.20 | 0.040 | 0.050 | 0.40 | —- | —- | 250 | 400 500 | 20 | Suitable for ordinary structural fabrication works where dynamic load is not required. |
ASTM A572 | gr 42 gr 50 gr 60 gr 65 | 0.21 0.23 0.23 | 1.35 1.35 1.35 1.65 | 0.040 0.040 0.040 0.040 | 0.050 0.050 0.050 0.050 | —- | —- | —- | 290 344 413 447 | 413 447 516 551 | 20 18 16 15 | Suitable for structural fabrication works where dynamic load is involved. |
IRS | M-41 | 0.10 | 0.25-0.45 | 0.0752 0.140 | 0.030 | 0.28-0.72 | Cu-.30.60 | —- —- | 340 —- | 480 —- | 22 —- | Suitable for the construction of railway wagons. |
DIN 17100 | qst 37.2 qst 44.2 qst 52.3 | 0.17 0.21 0.20 | —- 1.5 | 0.05 0.04 0.04 | 0.05 0.05 0.05 | —- —- 0.65 | —- | 90 90 | 235 275 355 | 340-470 410-510 490-640 | 26 22 22 | Suitable for ordinary structural works where dynamic load is not involved. |
Thickness (mm) | ≤5 | ≤10 | ≤15 | ≤20 | ≤25 | ≤30 | ≤40 | ≤50 |
Elongation (%) | 14 | 16 | 17 | 18 | 19 | 20 | 21 | 22 |
Rahim Weight Table of Plates:
Thickness | Weight of (8×4)’ Plate Approx. | Rft/MT | Cutting Size | Remarks |
06 mm | 140 Kgs | 50-52 | As per customer’s demand | Without End/Front/Side cuts |
07 mm | 163 kgs | 42-44 | “ | “ |
08 mm | 186 kgs | 36-38 | “ | “ |
09 mm | 210 kgs | 32-33 | “ | “ |
10 mm | 233 kgs | 30-32 | “ | “ |
11 mm | 256 kgs | 26-28 | ” | “ |
12 mm | 280 kgs | 24-26 | “ | “ |
16 mm | 930 kgs (full size) | 18-19 | Full Size/Single piece | Without End/Front Cuts |
20 mm | 930 kgs (full size) | 15-16 | “ | “ |
22 mm | 930 kgs (full size) | 13-14 | “ | “ |
25 mm | 930 kgs (full size) | 12-13 | “ | “ |
32 mm | 930 kgs (full size) | 9-10 | “ | “ |